Injection molding technology is the one used in the production of plastic and metal parts. This method of production is suitable for the mass production of parts where there is a repetitive production in thousands and millions of numbers.
The main apparatus for this production technology is the Injection Molding Machine which consists of several parts performing different functions to manufacture.
Let us have a look at the Injection Molding Machine parts and their functions:
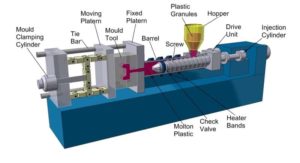
Let us look at the functions of its different parts
- Hopper As we can see the Hopper is a funnel-like structure where the material is fed into. The plastic material that goes into the hopper is in the form of pellets/grains. It is in the form of grains.
- Screw – The main function of this screw is to push the material towards the Heating zone and then towards the nozzle that goes through the fixed platern.
- Heater Bands – Heater bands help in melting the material which in turn helps in proper mixing of the material. The temperature maintained is between 280C to 350C.
- Nozzle – The function of the nozzle is to pour the material in the mold.
- Ejection Pins – These pins help in removing the product from the mold.
- Cooling Channel – These are used to cool off the material once it is in the mold so that It settles and takes the shape of the mold.
- Drive Unit – The drive unit consists of a motor whose function is to drive the screw which in turn pushes the material forward.
These are the main components of an Injection Molding Machine along with some secondary parts.
Pros of Injection Molding Technology
Rate of Production – The technology makes the production very quick and helps in delivering high amounts in less time.
Manpower – The requirement of manpower when using Injection Molding Technology is minimal. Hence, less manpower cost.
Mass Production – This technology is generally suitable for mass production as it delivers the products at very low cost when used for mass production.
Less Scrap – This production method leaves out very little scrap. Hence, less wastage leading to cost savings.
Finishing – The finish that injection molding technology provides to the parts is great and it requires very little effort in finishing works.
Now, let us have a look at some of the disadvantages.
Cons of Injection Molding Technology
Initial Cost – Initial machinery cost is quite high. Therefore, to start this business you need a significant amount of capital.
Cost of Molds – Since, different products have different molds and they have to be designed in a certain way, its cost is also on the higher side.
Mass Production – This method is beneficial only in mass production if you are looking for small volume production this technology might not be the right fit.
The Injection Molding Technology can be used in different variations according to the needs. Let us understand those variations and their purposes.
Types of Injection Molding Technology
Thin Wall Molding
To manufacture products having thin walls one makes use of the Thin wall Molding technique. These are generally suitable for the production of vessels, test apparatus, tubes, some electronic products, etc. The thin wall molding can be a complicated process as it requires strict supervision and design engineering to make sure the thin-walled product has suitable strength and durability. The main challenge in thin wall molding is to ensure the quality of products for which you can use vision systems to detect defects, cracks, etc.
Gas-Assisted Injection Molding
The gas-assisted injection molding is used in the production of parts having thick walls. Parts having thick walls are susceptible to deformation and also warping as the material cools down inside the mold. This deformation does not happen on filling gas in the mold containing the plastic material. This filling of gas facilitates a smooth outer surface while occupying the hollow space inside. Another advantage of this method is the at saves the cost of material as it requires lesser material.
Metal Injection Molding
Injection Molding Technology is not only for use in molding plastic but, metal products can also be manufactured by using this technology. The cost of metal molding is higher than the conventional methods of metal molding and also plastic molding. Markets like electronics, aerospace, mobile phones, etc. make use of metal injection molding.
Liquid Silicone Injection Molding
This method is the exact opposite of conventional injection molding where the heated material goes in a cold mold to form the parts. In silicone injection, the chilled silicone goes into a hot mold to take the shape. The major use of this method is in the manufacture of automotive parts, seals, medical apparatus, some of the electrical components, etc. Silicon imposes qualities like temperature resistance, electrical resistance, chemical resistance, etc. One con of silicone injection molding is that once it is formed, it cannot be brought back to a liquid state to remold.
3D Printing
3D printing is similar to or we can say it is a kind of injection molding technology itself. Its uses are in design reviews and prototyping of design. To understand and have a proper insight about a part before going into production face, companies are making use of 3D printing. One can make use of a 3D print model for discussion and finalizing of the part/mold with the client. This method is always better than 3D rendering. There are certain drawbacks in 3D printing at present but we expect in the future, the drawbacks will be eliminated.
Custom Material Injection Molding
Using different materials or the combination of different materials to impart specific properties is generally known as custom material injection molding. We can relate it somewhat to silicone injection molding as it provides different properties we have talked about. Similarly, for example, carbon is also used to inherit certain properties. You can add fillers and additives to modify the property of the product. Also, certain conditions have to maintained while adding different additives like temperature, quantity, etc. These are different for different materials.
Keep visiting us for more useful insights into the manufacturing industry. Do comment in the comment box if you have any questions or suggestions, we would love to hear from you.